انقلاب در اکتشاف و بهره برداری معادن با فناوری هسته ای - تسنیم
سنجش سریع درصد خلوص فلزات در سنگ معدن با فناوری هسته ای، انقلابی در فرآیندهای اکتشاف و بهره برداری معادن ایجاد کرده است.
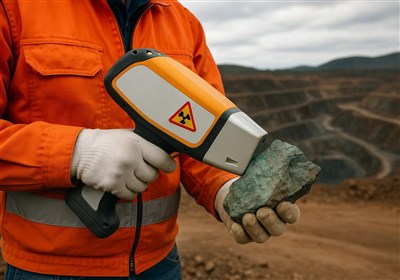
خبرگزاری تسنیم؛ گروه اقتصادی ــ یکی از چالشهای اصلی در صنایع معدنی، شناسایی سریع و دقیق میزان فلزات موجود در سنگهای معدنی است که به شکل مستقیم بر کیفیت اکتشاف، بهرهبرداری و فرآوری تأثیرگذار است.
سنتیترین روشها مبتنی بر نمونهبرداری و انتقال نمونهها به آزمایشگاههای تخصصی با هزینه و زمان زیاد هستند که این موضوع محدودیتهای جدی در روند تصمیمگیریهای عملیاتی ایجاد میکند.
فناوری هستهای با توسعه سیستمهای پرتودهی و آشکارسازی، امکان سنجش سریع درصد فلز در محل معدن (on-site analysis) را فراهم آورده است.
این فناوری، علاوه بر کاهش هزینه و زمان، از دقت و صحت مناسبی برخوردار است که آن را به ابزاری حیاتی برای مهندسان معدن تبدیل کرده است.
تجربه عملی و تحقیقات گسترده نشان میدهد که فناوریهای پرتودهی نوترونی و گاما میتوانند بهطور غیرمخرب و بدون نیاز به نمونهبرداری فیزیکی، ترکیب شیمیایی سنگها را با دقت قابل قبول در محل معدن تعیین کنند.
این رویکرد باعث تسریع در روند استخراج و افزایش بهرهوری میشود و در نتیجه، در بسیاری از پروژههای معدنی در سراسر جهان به عنوان یک استاندارد پذیرفته شده است.
مفهوم اساسی در این فناوری، استفاده از پرتوی نوترونی یا گاما برای تحریک هستههای اتمی در نمونه سنگ است.
بر اساس نحوه بازتاب، جذب یا نشر این پرتوها، میتوان عناصر مختلف و درصد آنها را اندازهگیری کرد.
این اندازهگیریها با تجهیزات پرتابل و قابل حمل انجام میشوند که طراحی شدهاند تا در شرایط دشوار محیط معدن کار کنند.
از جمله مزایای این فناوری، میتوان به کاهش چشمگیر خطاهای نمونهبرداری، افزایش سرعت تحلیل و قابلیت اجرای آن در زمان واقعی (Real-time) اشاره کرد که امکان واکنش سریع به شرایط متغیر معدن را فراهم میآورد.
بنابراین، سنجش سریع درصد فلز توسط فناوری هستهای، مسیر نوینی برای توسعه و مدیریت هوشمند معادن ایجاد کرده است.
معرفی و اصول کلی فناوری
فناوری هستهای در سنجش درصد فلزات بر پایه واکنشهای پرتویی هستهای استوار است.
دو نوع پرتودهی اصلی در این حوزه کاربرد دارند: پرتودهی نوترونی و پرتودهی گامای نوکلئیدی.
در روش پرتودهی نوترونی، نوترونها به هستههای اتمهای موجود در نمونه برخورد میکنند و باعث برانگیختگی هستهای میشوند.
سپس، هستهها در حال بازگشت به حالت پایدار، پرتوهای گاما با انرژیهای مشخصی ساطع میکنند که این انرژیها معرف نوع عنصر و میزان آن در نمونه هستند.
در روش پرتودهی گامایی، منبع پرتوزا پرتوهای گاما با انرژی بالا منتشر میکند که پس از عبور از نمونه، میزان جذب یا پراکندگی این پرتوها اندازهگیری میشود.
با تحلیل طیفی این دادهها، میتوان ترکیبات شیمیایی و میزان فلزات را تعیین کرد.
این فناوری بر مبنای اصل «طیفسنجی فعال پرتویی» کار میکند؛ یعنی نمونه به وسیله منبع پرتوزا تحریک میشود و پاسخ پرتویی آن تحلیل میگردد.
ابزارهای پرتودهی پرتابل امروزی قادرند با دقت بسیار بالا و در زمان کوتاه، اطلاعاتی چندعنصری استخراج کنند.
اصول کلیدی این فناوری عبارتند از: نفوذپذیری بالای پرتوها در مواد معدنی، قابلیت تشخیص عناصری با مقادیر اندک، و قابلیت کار در شرایط سخت محیطی.
این موارد باعث شده است که فناوری هستهای در تحلیل سنگ معدن، ابزاری منحصر به فرد و مطمئن باشد.
اجزای اصلی سیستم
سیستمهای سنجش سریع درصد فلز در محل معدن معمولاً از چند بخش اصلی تشکیل شدهاند که هر یک نقشی حیاتی در عملکرد کلی ایفا میکند.
بخش اول، منبع پرتوزا است که میتواند نوترونی یا گامایی باشد.
منابع نوترونی معمولاً از ایزوتوپهای همچون آم-برلیم (Am-Be) یا کلسیم-252 استفاده میشود که نوترونهای پرانرژی آزاد میکنند.
بخش دوم، آشکارساز پرتوی بازتابی است که وظیفه ثبت پرتوهای گاما یا نوترونی ساطع شده از نمونه را دارد.
آشکارسازهای نیمههادی مانند ژرمانیوم نیمههادی (HPGe) یا کریستالهای NaI(Tl) معمولاً استفاده میشوند که دقت بالایی در تفکیک انرژی پرتوها دارند.
کنترلکننده و پردازشگر دادهها، بخش سوم سیستم است.
این قسمت شامل سختافزار و نرمافزارهایی است که دادههای ثبت شده توسط آشکارساز را آنالیز و به شکل طیفهای انرژی تبدیل میکنند.
نرمافزارهای پیشرفته قادر به تفکیک عناصر مختلف و محاسبه درصد آنها در نمونه هستند.
محفظه یا پوشش حفاظتی و مکانیکی که تجهیزات را در برابر شرایط محیطی نظیر گرد و غبار، رطوبت و ضربه محافظت میکند.
این بخشها امکان استفاده از دستگاهها را در محیطهای دشوار معدنی فراهم میسازند.
از دیگر اجزای کمکی میتوان به باتریهای قابل شارژ، سیستمهای خنککننده و نمایشگرهای کاربری اشاره کرد که به عملکرد مستقل و مستمر دستگاه کمک میکنند.
فرآیند کلی انجام خالصسازی فلزات با پلاسما و پرتودهی
فرآیند خالصسازی فلزات با استفاده از پلاسما و پرتودهی، به شکلی مرحلهمند و مهندسیشده طراحی شده است تا بهینهترین مسیر حذف ناخالصیها را فراهم کند.
این فرایند معمولاً با آمادهسازی اولیه نمونه فلزی آغاز میشود.
بسته به نوع فلز و میزان ناخالصی، ممکن است عملیات پیشفرآوری همچون برش، ذوب جزئی یا قالبگیری صورت گیرد تا قطعه فلزی برای ورود به سامانه آماده شود.
در گام نخست، فلز در محفظهای مقاوم به دما و تابش قرار میگیرد.
سپس، سامانه پلاسما فعال میشود.
پلاسما که عمدتاً از گازهای خنثی تشکیل شده، در دمایی بسیار بالا تولید میشود و سطح فلز را تحت اثر مستقیم قرار میدهد.
این مرحله باعث گداخت جزئی یا تحریک سطحی فلز میگردد، بهگونهای که برخی ناخالصیهای سطحی شروع به تبخیر یا تجزیه میکنند.
در ادامه، سامانه پرتودهی وارد عمل میشود.
بسته به هدف فرآیند، از پرتوی نوترونی، گاما یا پرتوهای یونی بهرهگیری میشود.
این تابشها به عمق فلز نفوذ کرده و ساختار بلوری را تحریک میکنند.
انرژی پرتوی وارد شده، پیوندهای میان ناخالصیها و شبکه فلزی را سست کرده یا میشکند.
در برخی موارد، برای افزایش کارایی، گازهای واکنشی مانند هیدروژن، کلر یا نیتروژن به درون محفظه تزریق میشوند تا با ناخالصیها واکنش داده و به ترکیبات فرار تبدیل شوند.
در طول فرایند، حسگرهای طیفسنج، دما، فشار و تابش بهصورت لحظهای دادهها را ثبت و تحلیل میکنند.
این دادهها از طریق سیستم کنترل مرکزی، به الگوریتمهایی تحویل داده میشوند که پارامترهای تابش، جریان پلاسما و تزریق گاز را بهصورت پویا تنظیم میکنند.
این سامانه بسته به خروجی مورد نظر، میتواند فرآیند را در چند مرحله با شدتهای متفاوت تکرار کند.
پس از پایان تابش و قطع پلاسما، قطعه فلزی تحت سیستم خنککننده قرار میگیرد تا تنشهای حرارتی کاهش یافته و ساختار تثبیت شود.
در نهایت، نمونهها برای بررسیهای متالورژیکی، طیفسنجی عنصری و آزمون خلوص مورد ارزیابی دقیق قرار میگیرند.
در صورت نیاز، مراحل تکمیلی نظیر پولیش، شکلدهی نهایی یا بستهبندی در شرایط کنترلشده انجام میگیرد.
این فرآیند، گرچه نیازمند زیرساختهای فناورانه بالا و کنترل دقیق است، اما در مقایسه با روشهای سنتی، سرعت، دقت، و عمق پالایش بیشتری را ارائه میدهد و همزمان مصرف مواد شیمیایی را به حداقل میرساند.
انواع کاربردهای فناوری پلاسما و پرتودهی در خالصسازی فلزات
فناوری پلاسما و پرتودهی در خالصسازی فلزات، دامنهای گسترده از کاربردها را در صنایع گوناگون پوشش میدهد.
یکی از اصلیترین کاربردها، تصفیه فلزات استراتژیک نظیر تیتانیوم، نیکل، زیرکونیوم و نایوبیوم است؛ فلزاتی که بهواسطه کاربردشان در صنایع هوافضا، راکتورها، و سامانههای دفاعی، نیازمند خلوص بسیار بالا هستند.
در این موارد، پلاسما و پرتودهی نقش مهمی در حذف اکسیدها، نیتریدها و ناخالصیهای بینذرهای ایفا میکنند.
کاربرد دوم، در صنعت تولید آلیاژهای خاص است.
بسیاری از آلیاژهای نوین، تنها در صورتی عملکرد مناسب خواهند داشت که عناصر سازنده آنها در حد ppb (بخش در میلیارد) از ناخالصیهای مزاحم پاک شده باشند.
بهعنوان نمونه، آلیاژهای آلومینیوم-لیتیم یا آلیاژهای سوپرآلیاژ نیکل-کبالت، تنها با خلوص بالا میتوانند ویژگیهایی چون استحکام در دمای بالا، مقاومت در برابر خوردگی یا رسانش خاص را از خود نشان دهند.
از دیگر حوزههای کاربردی، میتوان به صنایع پزشکی اشاره کرد.
ابزارهای جراحی، ایمپلنتهای تیتانیومی و قطعات الکترونیکی زیستی، به دلیل تماس مستقیم با بدن، نیازمند حداکثر خلوص فلزیاند تا واکنش زیستی یا سمیت ایجاد نکنند.
فرآیندهای مبتنی بر پرتو و پلاسما، راهکاری ایمن برای دستیابی به این سطح از خلوص فراهم میکنند.
در حوزه تولید مواد اولیه برای صنایع نیمههادی و فوتونیک نیز این فناوری بسیار مهم است.
فلزاتی چون مس، آنتیموان، ژرمانیم، ایندیم و گالیم باید در شرایطی تولید شوند که کوچکترین ناخالصی، عملکرد تراشهها را مختل نکند.
پرتودهی کنترلشده، توانایی دارد ذرات مزاحم را از ساختار حذف کند و ساختاری کاملاً یکنواخت پدید آورد.
در نهایت، در حوزه بازیافت و احیای فلزات نیز پلاسما و پرتودهی بهکار گرفته شدهاند.
ضایعات فلزی یا محصولات برگشتی، معمولاً ترکیبات پیچیدهای از فلزات، آلیاژها و مواد غیرفلزیاند.
پرتودهی در کنار پلاسما، میتواند ساختار این ضایعات را تجزیه کرده و فلزات خالص را با راندمان بالا بازیابی نماید.
مزایای این روش نسبت به روشهای سنتی
فناوری پلاسما و پرتودهی در فرآیند خالصسازی فلزات، نه تنها از منظر علمی، بلکه در سطح صنعتی و اقتصادی نیز مزایای قابلتوجهی نسبت به روشهای سنتی دارد.
نخستین و مهمترین مزیت این روش، توانایی آن در حذف دقیق و هدفمند ناخالصیها بدون آسیبزدن به ساختار اصلی فلز است.
در حالی که روشهای سنتی نظیر اسیدشویی، احیا شیمیایی یا ذوب مجدد، معمولاً ناخالصیها را بهصورت غیرانتخابی حذف میکنند، فناوری پرتودهی و پلاسما امکان تمرکز بر گونههای خاص مزاحم را فراهم میسازد.
دومین مزیت، کاهش شدید مصرف مواد شیمیایی و ملاحظات زیستمحیطی است.
فرایندهایی نظیر شستوشوی اسیدی یا احیا با کمک کلر یا آمونیاک، علاوه بر ایجاد پسماندهای خطرناک، نیاز به تصفیه گسترده دارند.
در مقابل، فناوری پرتودهی یک روش پاک محسوب میشود که بهجای واکنشهای شیمیایی گسترده، از انرژی برای تحریک یا حذف ناخالصیها استفاده میکند.
سوم آنکه این فناوری موجب کاهش اتلاف فلزات پایه میشود.
در روشهای مرسوم، بخشی از فلز اصلی در جریان واکنش با مواد شیمیایی از بین میرود یا به همراه ناخالصیها دفع میشود.
اما در پرتودهی و پلاسما، چون هیچ واکنش مخربی بر روی شبکه فلزی انجام نمیشود، راندمان بازیابی فلز اصلی بالاتر است.
چهارم، سرعت بالای فرآیند است.
بهویژه در تولیدات انبوه و خالصسازی فلزات با ارزش بالا، کاهش زمان پردازش از ساعتها یا روزها به چند دقیقه، مزیت رقابتی محسوب میشود.
سامانههای پرتودهی پیشرفته قادرند ظرف چند ثانیه اثر مورد نظر را بر سطح یا حجم مشخصی از فلز اعمال کنند.
همچنین انعطافپذیری این فناوری در خالصسازی انواع فلزات، چه در حالت جامد، چه در حالت نیمهذوب یا پودری، امکان سفارشیسازی گستردهای را فراهم کرده است.
سامانههای پلاسما میتوانند متناسب با نوع فلز، دمای محیط و ویژگیهای مورد انتظار تنظیم شوند.
این امر باعث شده حتی فلزات فعال یا ناپایدار همچون تانتالوم یا هافنیوم نیز با این روش تصفیه شوند.
این فناوری از منظر اتوماسیون و قابلیت کنترل، مزیت بالایی دارد.
سامانههای نوین از حسگرها، الگوریتمهای یادگیری ماشین و کنترلرهای هوشمند بهره میبرند که باعث شده کیفیت خروجی در هر نوبت پردازش بهصورت یکنواخت و بدون انحراف حاصل شود.
در مجموع، این روش با حذف محدودیتهای روشهای سنتی، گامی مهم در جهت صنعتیسازی دقیق و پایدار فرآیند خالصسازی فلزات برداشته است.
چالشها و محدودیتهای فرآیند پلاسما و پرتودهی
اگرچه فناوری پلاسما و پرتودهی در زمینه خالصسازی فلزات تحولی چشمگیر پدید آورده، اما هنوز با چالشها و محدودیتهایی روبرو است که لازم است در توسعه و بکارگیری صنعتی آن مورد توجه قرار گیرد.
نخستین چالش، هزینه اولیه بالای تجهیز و راهاندازی این سامانههاست.
تولید پلاسما در دمای بالا، نیاز به ژنراتورهای توانمند، میدانهای مغناطیسی خاص و محفظههای خلأ مقاوم دارد.
همچنین سامانه پرتودهی با دوزهای کنترلشده نیازمند منابع پرتوزا یا شتابدهندههای پیشرفته است.
چالش دوم، نیاز به نیروی انسانی متخصص برای بهرهبرداری، تعمیر و کالیبراسیون این سامانههاست.
کار با پرتو، بهویژه در سطوح انرژی بالا، مستلزم رعایت دقیق پروتکلهای ایمنی، مهارت در اندازهگیری دوز، و تسلط به استانداردهای پرتوی است که در بسیاری از کشورها، محدودیت منابع انسانی متخصص وجود دارد.
از منظر فنی، یکی از محدودیتهای اصلی، یکنواختی اثر پرتودهی در قطعات بزرگ یا دارای هندسه پیچیده است.
چون تابش بهصورت خطی یا از یک منبع مرکزی اعمال میشود، گاهی برخی بخشها بیشتر یا کمتر از حد لازم تابیده میشوند و این عدم یکنواختی بر کیفیت نهایی اثر میگذارد.
همچنین در مورد برخی فلزات، میزان پاسخدهی به پرتو یا پلاسما متفاوت است و نیاز به تنظیمات اختصاصی دارد.
در حوزه زیستمحیطی نیز، اگرچه فناوری پلاسما خود پاک محسوب میشود، اما کار با پرتوهای یونساز نیاز به اقدامات حفاظتی، سیستمهای خنثیسازی و کنترل نشت دارد.
پسماند پرتوزا هرچند در مقیاس اندک، ولی باید طبق مقررات سختگیرانه مدیریت شود.
از دیگر محدودیتها، اندازه محدود محفظههای پردازش و هزینه عملیاتی نسبتاً بالا بهویژه در پردازش مقادیر کم میباشد.
این موضوع باعث شده فعلاً کاربرد این فناوری بیشتر در صنایع خاص و فلزات با ارزش بالا متمرکز باشد.
اما با پیشرفت فناوری، انتظار میرود هزینهها کاهش و ظرفیتها افزایش یابد.
استانداردها و دستورالعملهای بینالمللی
برای بهرهبرداری ایمن و مؤثر از فناوری پلاسما و پرتودهی در خالصسازی فلزات، رعایت استانداردهای بینالمللی الزامی است.
این استانداردها نه تنها جنبههای فنی فرایند، بلکه الزامات ایمنی، زیستمحیطی و کیفیت را نیز در بر میگیرند.
در حوزه پرتودهی، آژانس بینالمللی انرژی اتمی (IAEA) استانداردهای جامعی ارائه کرده است.
مستنداتی نظیر Safety Guide No.
SSG-46، استانداردهایی را برای استفاده صنعتی از منابع پرتوزا، حفاظت پرتو و کالیبراسیون دستگاهها تعریف کردهاند.
این استانداردها مشخص میکنند که دوز تابش مجاز برای انواع فلزات چقدر است، چه فواصل زمانی برای بازرسی مورد نیاز است و چه نوع آموزشهایی باید به اپراتورها داده شود.
در حوزه پلاسما، موسساتی چون ASTM International، استانداردهایی را در زمینه تولید و کنترل پلاسما در فرآیندهای صنعتی منتشر کردهاند؛ از جمله ASTM E238-18 که روش اندازهگیری خواص پلاسمای قوسی برای فرآیندهای متالورژیکی را توصیف میکند.
همچنین ISO 9001 بهعنوان چارچوب سیستم مدیریت کیفیت، در تمامی مراحل طراحی و اجرای فرآیند باید رعایت گردد.
برای تضمین کیفیت فلز خالصشده، استفاده از روشهای آزمون غیرمخرب (NDT) مطابق با استانداردهای ISO 17637 (بازرسی چشمی)، ISO 10893 (آزمون فلزات) و ISO 11484 (مستندسازی نتایج آزمون) توصیه شده است.
در حوزه ایمنی، استانداردهای IEC و ICRP الزامات حفاظتی برای کار با تجهیزات پرتودهی را تدوین کردهاند.
برای نمونه، استاندارد IEC 60601 در مورد حفاظت از اپراتورها در برابر پرتوهای یونساز، و توصیههای ICRP Publication 103 در مورد حدود مجاز پرتوگیری اپراتورها مورد استناد است.
در مجموع، بهرهبرداری از فناوری پلاسما و پرتودهی در خالصسازی فلزات نیازمند انطباق کامل با مجموعهای از استانداردهای چندبعدی بینالمللی است.
این انطباق تضمین میکند که فرآیند از نظر کیفی، ایمنی و زیستمحیطی در بالاترین سطح انجام گیرد و خروجی آن بتواند وارد زنجیره تأمین جهانی شود.
پیشرفتهای نوین این روش
در سالهای اخیر، فناوری پلاسما و پرتودهی در حوزه خالصسازی فلزات با پیشرفتهایی همراه بوده که آن را از یک ابزار علمی به یک فناوری صنعتی مؤثر بدل کرده است.
یکی از مهمترین دستاوردها، استفاده از سیستمهای پلاسما با منبع مایکروویو است که بهجای استفاده از قوسهای الکتریکی یا تخلیه جرقهای، از تابش مایکروویو برای تحریک مولکولهای گاز استفاده میکند و امکان دستیابی به پلاسماهای پایدار در دمای پایینتر را فراهم میسازد.
این فناوری بهویژه برای فلزات حساس به گرما بسیار کارآمد بوده است.
همچنین، توسعه سیستمهای پرتودهی با دوز متغیر و کنترلشونده از طریق الگوریتمهای یادگیری ماشین، گامی بزرگ در بهبود دقت و تکرارپذیری فرایند محسوب میشود.
این سامانهها قادرند بهصورت بلادرنگ خواص فیزیکی نمونه فلزی را اندازهگیری و متناسب با آن میزان و مدت تابش را تنظیم کنند.
پیشرفت دیگر، توسعه سیستمهای پرتودهی قابلحمل و مینیاتوری برای استفاده در محیطهای معدنی و صنعتی است.
این تجهیزات با بهرهگیری از شتابدهندههای الکترونی کوچک و منابع پرتو ایزوتوپی با حفاظهای سبک، به اپراتور اجازه میدهند بدون نیاز به جابجایی نمونه، عملیات خالصسازی را در محل انجام دهد.
در زمینه ترکیب فناوریها، هماکنون پروژههایی در حال اجراست که استفاده توأمان از پرتو و پلاسما را با نانوپوششهای سطحی ترکیب میکنند.
در این فرایند، ابتدا خالصسازی انجام شده و سپس سطح فلز با پوششهایی از جنس کربن الماسی (DLC) یا نیترید تیتانیوم پوشانده میشود تا از اکسیداسیون و آلودگی مجدد جلوگیری گردد.
در سطح علمی نیز مدلسازی عددی دقیق رفتار الکترونها و یونها در پلاسمای غنیشده، امکان بهینهسازی ساختار را از پیش فراهم میسازد.
دانشگاههای فنی نظیر MIT، ETH Zurich و توکیو تک، با استفاده از شبیهسازهای الکترومغناطیسی، توانستهاند طراحیهایی برای همگرایی بهتر پرتوها در سامانههای پرتودهی پلاسما-محور ارائه دهند که راندمان نهایی را تا 30 درصد افزایش داده است.
این پیشرفتها در کنار تولید منابع پرتوی پایدارتر، کاهش مصرف انرژی، و تولید دستگاههایی با مصرف گاز پایینتر، نویدبخش آیندهای هستند که در آن، خالصسازی فلزات با پلاسما و پرتو نهتنها اقتصادیتر، بلکه ایمنتر، سریعتر و با بازده بالاتر خواهد بود.
آیندهنگری و توصیهها
با توجه به روندهای جهانی در حوزه کاهش مصرف مواد شیمیایی، افزایش بهرهوری صنعتی، و تقاضای روزافزون برای فلزات با خلوص بالا در صنایع نوین، آینده فناوری پلاسما و پرتودهی در خالصسازی فلزات بسیار روشن بهنظر میرسد.
این فناوری میتواند یکی از ارکان تحولساز در صنعت متالورژی قرن بیستویکم باشد.
در افق آینده، انتظار میرود که این فناوری از انحصار صنایع پیشرفته خارج شده و بهتدریج در صنایع متوسط و حتی معادن مناطق کمتر توسعهیافته نیز نفوذ کند.
اما تحقق این هدف مستلزم سیاستگذاریهای هوشمندانه، آموزش گسترده نیروی انسانی، و حمایت از بومیسازی تجهیزات است.
دولتها و دانشگاهها باید در جهت ایجاد خوشههای فناوری با تمرکز بر پرتودهی صنعتی و سامانههای پلاسما، سرمایهگذاری بلندمدت داشته باشند.
از منظر صنعتی، توصیه میشود که شرکتهای فعال در حوزه فرآوری فلزات، بهویژه فلزات کمیاب و با ارزش بالا، از همین امروز در زمینه آزمایشهای پایلوت و تطبیق فناوری پرتودهی با محصولات خود اقدام کنند.
انتخاب دقیق نوع منبع پرتوی، تنظیمات میدان پلاسما و طراحی تجهیزات اختصاصی برای هر خط تولید، از ضروریات بهرهبرداری موفق است.
در سطح بینالمللی نیز، توسعه همکاریهای فناورانه و انتقال دانش بین کشورهای پیشرو و در حال توسعه میتواند به کاهش هزینهها و بهبود عملکرد این فناوری بینجامد.
ایجاد پایگاههای داده مشترک از نتایج پرتودهی، مستندسازی دقیق تجربیات و طراحی الگوریتمهای هوشمند تنظیم سامانهها، همگی در این مسیر نقشآفریناند.
آینده متعلق به فناوریهایی است که با سرعت، دقت و پاکی، پاسخگوی نیازهای صنعتی باشند.
پلاسما و پرتودهی، با کنار زدن محدودیتهای روشهای سنتی، این قابلیت را دارند که به ستون فقرات صنایع خالصسازی فلزات در جهان فردا تبدیل شوند.
جمعبندی
فناوری پلاسما و پرتودهی در خالصسازی فلزات، در دهه اخیر به یکی از شاخصترین نوآوریهای فنی در حوزه متالورژی بدل شده است.
این فناوری با ترکیب علم فیزیک هستهای، مهندسی مواد، و فناوری اطلاعات، پاسخی پیشرو به چالشهایی چون مصرف بالای مواد شیمیایی، بازده پایین روشهای سنتی، و نیاز روزافزون به خلوص بالا در صنایع پیشرفته ارائه داده است.
توسعه این فناوری هم توانسته استانداردهای صنعتی را ارتقاء دهد، و هم با کاهش مصرف انرژی، کاهش ضایعات و آلایندهها، و افزایش سرعت تولید، پاسخگوی مقتضیات عصر صنعت سبز نیز بوده است.
چه در خالصسازی فلزات پایه مانند مس و روی، و چه در پالایش فلزات کمیاب و فوقخالص نظیر ایریدیوم، تانتالوم و نئودیمیوم، پلاسما و پرتودهی با دقت، سرعت و پایداری عمل کردهاند.
البته مانند هر فناوری نوپا، چالشهایی نیز مطرح است؛ از هزینه اولیه بالا تا نیاز به نیروی انسانی متخصص و رعایت دقیق استانداردهای ایمنی.
با این حال، روند جهانی سرمایهگذاری در این حوزه، نشان از اعتماد به آینده درخشان آن دارد.
بسیاری از کشورها، مراکز تحقیقاتی و شرکتها، توسعه این فناوری را در دستور کار قرار دادهاند.
برای کشورهای در حال توسعه، بهرهگیری از این فناوری میتواند ابزار راهبردی برای جهش صنعتی و کاهش وابستگی به واردات فلزات خالص باشد.
اگر سیاستگذاران، دانشگاهها و صنعتگران با نگاهی بلندمدت، زمینه بومیسازی، آموزش و استقرار زیرساختها را فراهم آورند، در آیندهای نهچندان دور، شاهد تولید فلزات فوقخالص در مقیاس صنعتی و صادراتی خواهیم بود.
پلاسما و پرتودهی، بهمثابه نماد تلفیق علم و صنعت، افقی نو برای آینده متالورژی ترسیم کردهاند؛ افقی که در آن، خلوص دیگر یک آرمان پرهزینه نیست، بلکه دستاوردی در دسترس، پایدار و اقتصادی است.
انتهای پیام/